Welcome to the fascinating journey of a countertop, a story often untold but integral to the charm and functionality of our homes. Imagine a piece of raw stone, nestled in the earth’s crust, destined to transform into a beautiful and functional centerpiece in your kitchen or bathroom.
This journey, from the depths of a quarry to the heart of your home, is not just a tale of manufacturing but also an art form that blends nature, craftsmanship, and technology. Let’s embark on this adventure together, unraveling the steps and processes that turn a rugged rock into the sleek, polished surface that enhances the aesthetic of your living space.
Understanding the Origins: The Quarry
The story of a countertop begins long before it reaches a home, starting deep within the earth at quarries, the birthplaces of the beautiful stones we admire in our kitchens and bathrooms. Quarries are fascinating places where the beauty of natural stone is in its most raw and untouched form.
Types of Stone Used for Countertops
Quarries around the world are home to a variety of stones that eventually make their way into our homes. The most popular choices include:
- Granite: Known for its durability and unique grain patterns.
- Marble: Valued for its timeless beauty and elegance.
- Quartzite: Offers a look similar to marble but with greater durability.
- Limestone and Travertine: Loved for their earthy tones and natural textures.
- Soapstone: A dense stone, known for its non-porous properties and matte finish.
Each type of stone has its own unique properties and aesthetics, making the selection a personal choice for homeowners.
Quarrying Process
The process of quarrying is both an art and a science, involving careful planning and execution. It begins with identifying a site where quality stone is abundant. Geologists play a key role in this, using their expertise to locate the best sources.
Once a site is selected, the quarrying process can begin. This involves several steps:
- Drilling and Cutting: Large blocks of stone are cut from the earth using specialized equipment. Techniques vary from traditional drilling and cutting to advanced methods using diamond-tipped wires and saws.
- Extraction: The cut stone blocks are then carefully extracted to minimize damage. Cranes and other heavy machinery are typically used for this purpose.
- Transportation: Extracted blocks are transported from the quarry site to processing facilities. This step requires meticulous planning to ensure the safety and integrity of the stone.
The quarrying process is a testament to human ingenuity and respect for natural resources. It’s a delicate balance between extracting valuable materials and preserving the integrity of the landscape. As we delve deeper into the journey of a countertop, we gain a greater appreciation for the effort and expertise involved in bringing these natural treasures into our homes.
Extraction Techniques
The extraction of stone from quarries is a critical step in the journey of a countertop. This process has evolved over centuries, from primitive manual methods to highly sophisticated techniques, ensuring efficiency, safety, and minimal environmental impact.
Traditional Methods
In the past, quarry workers used simple tools like hammers, chisels, and wedges to extract stone. These methods required immense physical labor and were time-consuming. The precision was largely dependent on the skill and experience of the workers. Traditional techniques, while less common now, are still used in some parts of the world, especially in areas where the unique characteristics of the stone demand more delicate extraction methods.
Modern Technology in Stone Extraction
Advancements in technology have revolutionized stone extraction in quarries:
- Diamond Wire Cutting: This method uses a wire embedded with industrial diamonds to cut through stone. It allows for precise cuts with minimal waste and is less labor-intensive compared to traditional methods.
- Water Jet Cutting: High-pressure water jets, sometimes mixed with abrasive materials, are used to cut through stone. This method is known for its precision and ability to cut complex shapes.
- Explosives: In some quarries, controlled explosions are used to break large blocks of stone from the earth. This technique is carefully managed to ensure safety and minimize damage to the stone.
- Heavy Machinery: Bulldozers, excavators, and cranes are often employed to move large stone blocks. This machinery has made the extraction process faster and more efficient.
- Remote Monitoring and Drones: Modern quarries often use drones and remote monitoring technology to survey the site, plan extraction, and ensure safety.
These modern techniques have not only increased efficiency but also reduced the environmental impact of quarrying. By maximizing the yield from each block of stone and minimizing waste, these methods are more sustainable and environmentally friendly.
The extraction of stone is a blend of art and science. It requires a deep understanding of the material, precision in execution, and respect for the natural environment. The techniques employed in this stage significantly impact the quality of the final product, highlighting the importance of expertise and technology in the journey of creating a countertop.
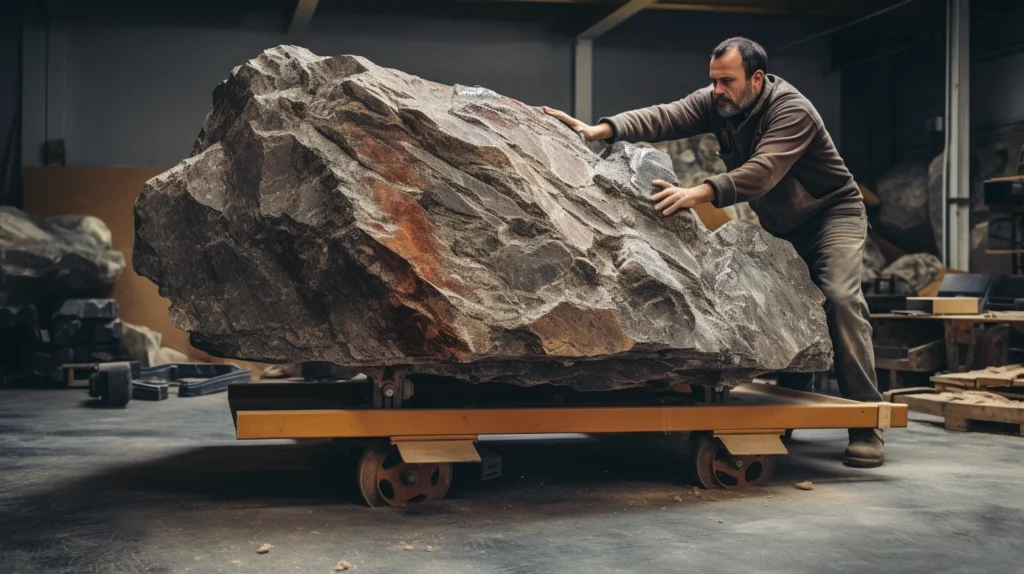
Transporting the Raw Stone
Once the stone is successfully extracted from the quarry, the next crucial phase is its transportation to processing facilities. This stage is as important as the extraction itself, as it involves moving massive blocks of stone over potentially long distances while ensuring their integrity and safety.
Logistics and Challenges
The logistics of transporting raw stone are complex and require meticulous planning. The challenges include:
- Weight and Size: Natural stone blocks are extremely heavy and large, demanding specialized transportation methods. Heavy-duty trucks and trailers are commonly used for this purpose.
- Road Transportation: Navigating roads with oversized loads requires careful route planning to avoid low bridges, narrow roads, or areas with weight restrictions. Special permits are often required for such transportation.
- Handling and Loading: The process of loading and unloading these heavy blocks demands precision and care. Cranes and forklifts are typically used, and the process is overseen by skilled personnel to avoid any damage.
- International Shipping: If the stone is sourced from overseas, it involves shipping by sea or air. This adds layers of complexity in terms of customs, import regulations, and additional handling.
- Safety Considerations: Ensuring the safety of both the transport team and the public is paramount. This involves adhering to strict safety standards and regulations.
Protecting the Stone
Protecting the stone during transit is critical. This includes:
- Secure Packaging: The stone is often wrapped or covered to protect it from weather elements and road debris.
- Stabilization: Ensuring the stone is stable and secure on the transport vehicle to prevent any movement that could cause cracks or breaks.
- Insurance: Transporting such valuable cargo usually involves comprehensive insurance to protect against any unforeseen incidents.
Transporting the raw stone from the quarry to the processing facility is a journey that requires expertise, careful planning, and respect for the material. The efforts put into this phase ensure that the stone arrives in the best possible condition, ready for the next stage of its transformation into a beautiful countertop.
The Art of Stone Processing
After the arduous journey from the quarry to the processing facility, the raw stone undergoes a transformation into the elegant countertops we see in homes. This phase, often referred to as the art of stone processing, involves several meticulous steps.
Cutting and Shaping
- Initial Sizing: The first step is to cut the large blocks into more manageable sizes. This is typically done using large saws, like gang saws or block cutters, which can handle the stone’s size and hardness.
- Slab Cutting: The sized blocks are then sliced into slabs using high-precision machinery. The thickness of the slabs depends on their intended use and customer preference.
- Shaping and Edging: Once cut into slabs, the stone is shaped and edged. This can involve cutting the slabs into specific shapes for countertops or adding decorative edges. Computer Numerical Control (CNC) machines are often used for this purpose, ensuring precision and consistency.
Polishing Techniques
- Surface Polishing: The slabs are then polished to achieve the desired finish, whether glossy, matte, or textured. This is done using abrasive materials and polishing pads in a sequential manner, moving from coarser to finer grains.
- Detailing and Finishing: The final touches are added, such as honing or sealing the surface. This not only enhances the stone’s appearance but also protects it from stains and scratches.
Quality Inspection and Selection
After processing, each slab undergoes a thorough quality inspection. This includes checking for:
- Structural integrity: Ensuring there are no cracks or significant natural flaws.
- Aesthetic appeal: Confirming the color and pattern meet quality standards.
- Finish quality: Ensuring the polish or honing is consistent across the slab.
Only the slabs that pass these rigorous quality checks are deemed ready for the market.
The art of stone processing is a blend of traditional craftsmanship and modern technology. It requires skilled artisans and technicians who understand the nuances of different types of stone. The transformation from a rugged, raw block of stone into a polished, sophisticated slab is a testament to the skill and dedication involved in this process, bringing us one step closer to having these natural masterpieces in our homes.
Quality Inspection and Selection
After the intricate process of cutting, shaping, and polishing, the stone slabs are ready for the critical phase of quality inspection and selection. This stage is pivotal in ensuring that only the best quality countertops reach customers.
Criteria for Quality
Quality inspection of stone slabs involves several criteria:
- Integrity and Strength: Inspectors check for cracks, fissures, and structural weaknesses. A slab with such flaws is less durable and more prone to damage during installation or use.
- Surface Uniformity: The surface of the slab should be uniformly polished without any uneven textures or marks. This includes checking for consistency in glossiness or matte finish, as per the design specifications.
- Color and Pattern Consistency: Natural stone varies in color and pattern. Inspectors ensure that slabs, especially those intended to be installed side by side, have matching or complementary patterns and colors.
- Thickness Consistency: The slab’s thickness should be consistent throughout to ensure a level installation and structural integrity.
- Edge Quality: The quality of the edges, whether beveled, rounded, or squared, is also inspected for uniformity and smoothness.
Selection Process
Once the slabs pass the quality inspection, they move to the selection process:
- Sorting by Quality and Aesthetics: Slabs are sorted into categories based on quality and aesthetics. This helps in matching them to various market needs and price points.
- Customer Preferences: Customers often have specific preferences for their countertops in terms of color, pattern, and finish. During selection, these preferences are taken into account, ensuring that each customer receives a product that aligns with their vision and interior design.
- Application Suitability: Certain types of stone are more suited for specific applications (e.g., high-traffic areas, moisture-prone spaces). The selection process also considers these factors.
Quality inspection and selection are about more than just ensuring the absence of defects; it’s about preserving the natural beauty and integrity of the stone while aligning it with customer expectations and needs. This careful scrutiny and meticulous selection process guarantee that the countertops not only add aesthetic value to homes but also stand the test of time in terms of durability and functionality.
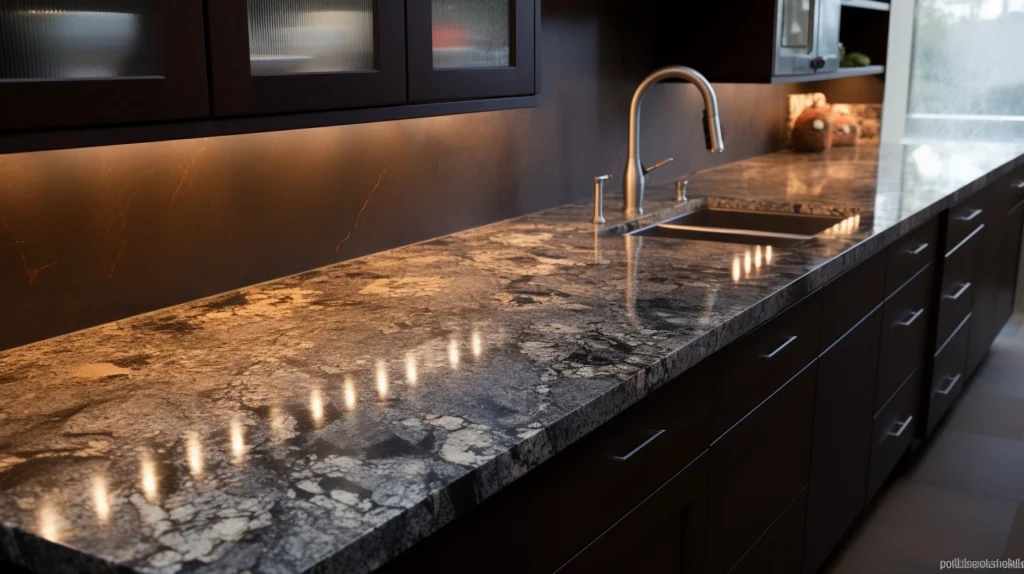
Installation: The Final Step
The journey of a countertop culminates in its installation, a critical phase where the beautifully crafted stone finally finds its place in a home. This step requires precision, skill, and attention to detail to ensure that the countertop is not only aesthetically pleasing but also functional and durable.
Preparation and Precautions
- Site Assessment: Before installation, a thorough assessment of the installation site is necessary. This includes measuring the space, checking for level surfaces, and ensuring the cabinetry can support the weight of the stone.
- Template Creation: A template of the countertop area is created to ensure an accurate fit. This template accounts for sink placement, faucets, and any other fixtures.
- Transport to Site: The stone slabs are transported to the installation site with utmost care to prevent any damage.
Installation Process
- Laying the Foundation: A strong base or support is crucial for the countertop. This might involve reinforcing existing cabinetry or building additional support structures.
- Fitting the Slab: The slab is carefully lowered onto the base. It’s crucial to ensure that it aligns perfectly with the template and the space.
- Securing the Countertop: Once in place, the countertop is secured using adhesives and sealants. This step is vital for stability and to prevent any movement that could lead to cracks or damages.
- Finishing Touches: After the countertop is secured, finishing touches like sealing the stone, adding backsplashes, and finishing edges are completed. Sealing is particularly important for porous stones like marble to prevent staining and facilitate easy cleaning.
- Inspection and Cleaning: The final step is a thorough inspection to ensure quality and precision in installation. Following this, the countertop is cleaned and polished, revealing its full beauty and luster.
Safety and Professionalism
Professional installers who are experienced and skilled in handling stone should carry out the installation. They are equipped with the right tools and knowledge to handle the weight and intricacies of stone countertops. Safety for both the installers and the household is a top priority throughout the process.
The installation of a countertop is not just the conclusion of its physical journey but also the beginning of its life as a central, functional, and aesthetic part of a home. The care and expertise invested in this final step ensure that the countertop is not only a visual delight but also a durable and integral part of the daily life within the home.
Conclusion
The journey of a countertop, from a rugged quarry to the heart of your home, is a remarkable story of transformation. It starts with the careful extraction of stone, embodying centuries of geological history, and culminates in the skilled artistry of crafting a functional and beautiful surface that enhances the aesthetics of our living spaces.
Throughout this journey, we witness a harmonious blend of nature’s beauty with human ingenuity. From the quarrying process that respects the stone’s natural form, to the precision of modern cutting and polishing techniques, every step reflects a deep understanding and appreciation for this natural resource.
The careful transportation, meticulous quality inspection, and selection processes ensure that only the best slabs make their way into homes. And finally, the skillful installation of these countertops brings this journey full circle, as these stones serve their purpose in kitchens and bathrooms, adding elegance and functionality to daily life.
This journey is not just about creating a product; it’s about crafting a legacy that merges natural beauty with human craftsmanship. As we use and admire these countertops in our homes, we become a part of this timeless narrative, a testament to the enduring bond between nature and human creativity.